An Unbiased Comparison of Linear BL Technologies
Disclaimer
The first thing I must make abundantly clear is that, though I feel all information listed below is highly accurate, it is possible I am wrong in certain areas. Let’s face it: I’m human. Though the concepts are well understood, much of what I discuss is my interpretation and opinion on a given set of circumstances. I come into this with absolutely zero bias and I feel that gives this more validity than other comparisons of a similar nature that you may have read. Above all, please read in the interest of gaining another viewpoint.
Table of Contents
1.0 - Prelude
2.0 - Split-Gap
3.0 - LMT (Linear Motor Technology)
4.0 - Split Coil
5.0 - Efficiency/Flux Efficiency
6.0 - BL Linearity
7.0 - Inductance
8.0 - Power Handling
9.0 - Scalability
10.0 - Manufacturing Tolerances
11.0 - Manufacturing Costs
12.0 - Conclusion
Prelude
In case the title is insufficient in describing the concept here, I’ll briefly explain it. There are currently three well-known methods of achieving linear BL product. If you’re not sure why this is important, please read the Understanding Power Compression thread. This treatise of sorts will be a method of comparing the three primary technologies (hereto referred to as “gap treatments”). I cannot stress this enough:
There is no “best” gap treatment.
If you have a particular design in mind, there may be one particular gap treatment that will work best for that design, but in no way does that mean it is always the best option. As such, I will be outlining the differences from one gap treatment to another by comparing their value in various aspects rather than comparing the gap treatments as whole pieces. At the end, I will try to summarize what situation(s) each gap treatment is most likely to provide positive results in. Let’s start with a history of each, shall we?
Note: I attempted to provide a quick and crude visualization of what each gap treatment looks like. Please forgive me if the drawings aren’t perfect.
Split-Gap
This is a fairly (in)famous gap technology that many of you will already be aware of. Originally patented as XBL^2 by Daniel Wiggins and David Hyre (formally of Adire Audio/Extremis Audio, now of Acoustic Development Technologies), this is now being referred to (and trademarked) as Split-Gap, which is a much more accurate and understandable term. The term indicates exactly what you see pictured below:
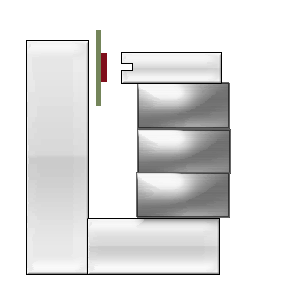
As you can see, there is a notch of sorts that is machined into the top plate. If we forget about the notch for a moment, the speaker appears to be underhung (meaning the coil height is shorter than the gap height), though it is very close to being evenhung (meaning both the coil and the gap are of the same height). However, that little notch in the top plate makes the speaker behave in a different method than both underhung and evenhung. As the speaker moves, an equal amount of windings enter one region of the gap as the number of windings that exit the other gap. This gap treatment can be found in a large number of past and present speakers, including many products from Adire Audio, Creative Sound Solutions, Blueprint, Ascendant Audio, and many others. It is worth noting that of those 4 companies I listed, two no longer exist and one switched from using split-gap a few years ago. However, in no way does that represent the abilities of the technology.
LMT (Linear Motor Technology)
This gap treatment is growing in popularity. This treatment is a clever one designed and patented by Thilo Stompler of TC Sounds. If the name rings a bell, it’s because TC Sounds does OEM work for several companies. This technology is a few years old now and likely to be featured in future OEM and direct sales products from TC Sounds in the future. See the image below:
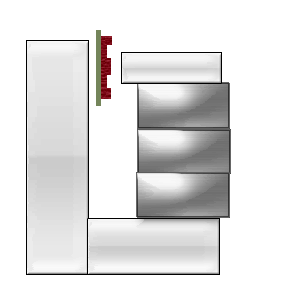
You’ll notice that the top plate is not machined in any way. TC Sounds manipulates BL through the speaker’s stroke by utilizing a variable density coil. In layman’s terms (and in case the image does not make this clear), the voice coil has varying layers of windings at different sections along the former. By adding more coil at the upper and lower limits, BL is higher than on a typical speaker when the coil approaches the outer limits of the gap. This gap treatment is featured on products from SoundSplinter (Rl-s), Eclipse (SW8200), and some direct offerings from TC Sounds (most notably, the LMS-5400).
Split Coil
From what I can find via research, the concept of a split coil is roughly 3 decades old. Though there has been seemingly little interest in this gap treatment for many years, it is also increasing in popularity, due in part to a desire to achieve higher excursion levels while keeping BL linear, and in part to Scott Atwell’s utilization of the technology on a few very popular designs of late. If you haven’t already heard, Scott Atwell was the very talented engineer at Resonant Engineering (and the Destijl buildhouse), who has since moved on to Fi Car Audio (and its associated buildhouse). Of the three gap treatments listed here, Split Coil is the only one that is not covered via a patent, pending or otherwise. The concept, as you can see below, is pretty much the opposite of the Split-Gap concept.
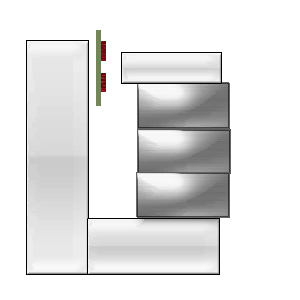
Here we have no modifications to the top plate, nor do we have varying layers of windings on the voice coil. Instead, we have some of the voice coil located in the upper region of the gap with some of the voice coil located in the lower region of the gap, with a noticeable split between the two sections. As the speaker begins to move, an equal number of windings enter the gap as the number that exit. Pretty easy to grasp, I think. Perhaps the two best examples of speakers that utilize Split Coil would be the Resonant Engineering XXX (with an obscene 54mm of Xmax) and the Ascendant Audio Poly 6.5” (with an equally impressive 11mm of linear one-way excursion). I would expect to see more split coil designs in the not-too-distant future.
With the preliminary (and important) background information out of the way, let’s move on to the areas that I have identified as “relevant” to speaker design.
Efficiency/Flux Efficiency
Looking at the title of this section, you may be thinking “Did he just say the same thing twice?” Actually, I haven’t at all, and this is one of the keys to differentiating between the technologies. When one of the original comparisons of gap treatments first came out, there was some very clever wording used. The poster often referred to flux efficiency and efficiency in similar posts, giving many the impression that they were virtually one and the same. The fact is that they are not necessarily the same at all. Let’s break that concept down for a moment.
The term flux efficiency refers to how efficiently the flux in the motor is used. I know, weird. This concept is very simple: a given length of voice coil in the gap (L) is capable of integrating with a given magnetic field density or strength (B ). If L is too short, the flux capability of B will not be full utilized. This would be an example of low flux efficiency.
Efficiency of a speaker, on the other hand, is very different. A highly efficient speaker does not necessarily need the best flux efficiency. For example, a speaker with low B and small L while having high Mms (moving mass), will still be inefficient, even though it is possible that flux efficiency is very high. Hopefully that’s clear as mud.
So which gap treatment is the best? Well, let’s look at flux efficiency first. In case you were unaware, all of the B does not lie in the gap: there is some B in what’s called the “fringe field”, or more easily understood as the outer limits of the gap. If you wanted to achieve very high flux efficiency, you would ideally have a coil that is able to use all of the B in the gap AND all of the B outside of the gap. Of course, that’s near impossible to do. But which gap treatment does it the best? That’s likely Split-Gap. Split Coil does a great job of utilizing B in the fringe field, but sacrifices some of the B integration in the middle of the gap. LMT requires a larger gap than typical due to the variable layers of windings (to avoid scraping coil in the gap during its travel). So Split-Gap should be the most efficient design, correct? Nope.
Remember that notch that Split-Gap has? Guess what: it actually sacrifices some B, similar to how the wider gap required for LMT sacrifices some B. The further you move the top plate from the coil, the less B is utilized. So when you machine a notch in the gap, you are giving up B. This will actually drop your speaker’s efficiency, even though you have likely increased flux efficiency. Split Coil, though it is less flux efficient, does not sacrifice any B from the top plate at all. Likewise, LMT does not do so either. Split-Gap is likely the least efficient design from this standpoint. These issues can be overcome by adding more to the magnet structure, though this is pointless once you have saturated the top plate. You could make a taller top plate if you’d like, but this grows increasingly expensive and it is harder to achieve a consistent magnetic field through a tall top plate. Split Coil drops efficiency because it intentionally sacrifices the most dense flux (in the middle of the gap) for the least dense flux (in the fringe field). LMT sacrifices efficiency because the gap needs to be wider to accommodate the thicker layers of windings at various points in the coil.
The last part of the speaker efficiency equation is the moving mass of the speaker. Forget about the other soft parts for a moment and think only of the voice coil’s role here. Split-Gap uses the smallest voice coil, so it’s moving mass is the lowest. Split coil generally uses a smaller voice coil than LMT (though this depends on the number of windings on the LMT coil) and thus has the second lowest moving mass. LMT usually has the highest moving mass. However, minor differences in the moving mass pale in comparison to large changes in the BL of a speaker.
In conclusion, Split-Gap is the most flux efficient design. However, Split Coil will likely result in the most efficient speaker, followed by LMT, and, lastly, Split-Gap.
BL Linearity
All three gap treatments very clearly help to linearize BL over a speaker’s stroke; there is no arguing that. But are all the gap treatments equally linear over long distances? Which gap treatment is easy to achieve ridiculous levels of linear BL? The answer here is very simple.
If you’re familiar with underhung vs. overhung arguments, you’re likely aware that, while underhung designs are capable of more linear BL, they are very hard to achieve linear BL over a very large stroke at an affordable price. Remember how I mentioned that tall top plates can get pricey with inconsistent magnetic field strength? These disadvantages come directly into play with an underhung speaker, and sadly, making taller and taller top plates is the only way to achieve more stroke with an underhung design. This same argument is very applicable when comparing the three gap treatments we’re looking at.
Split-Gap uses a coil that is smaller in height than the height of the gap and suffers from the same effects outlined above for underhung speakers. If you want really huge stroke from a Split-Gap speaker, be prepared to fork over some cash for your top plate. Oh, and make sure that you have a good magnet structure to keep that top plate as saturated as possible. Another consideration: by machining a notch in the top plate, Split-Gap sacrifices some BL at rest. This can be controlled by working with the depth of the notch in your top plate, but is clearly visible in many Klippel and Dumax results for Split-Gap speakers, where there is a plateau of sorts at rest and then BL product rises once the coil begins to move in the forward and rearward directions. LMT and Split Coil, on the other hand, fall more within the realm of overhung speakers. If you want to add more stroke, add more coil height. As the coil gets taller and taller, the backplate needs to be moved further and further back on the speaker. Here, the use of double or triple stack magnet structures proves much more affordable than machining a very tall top plate. It’s easy to get the stroke and gain the clearance with Split Coil and LMT. Now it’s worth noting that because LMT allows the manufacturer to customize the layers of windings at various points in the coil, the voice coil can theoretically be designed for an absolutely obscene amount of stroke AND LMT will allow the speaker engineer to carefully guarantee ruler flat BL until the entire coil has left the gap. Split Coil, on the other hand, will see BL begin to drop slowly as it reaches its outer excursion limits. Still, it is very capable of huge excursion without a very tall top plate.
All things considered, the LMT is probably the best for huge stroke with perfectly flat BL. Split Coil is next, with Split-Gap usually bringing up the rear.
Inductance and Inductance Variation
This is a key factor in many speaker designs. Inductance (Le as a thiele/small parameter) is a key limiter in the bandwidth of a speaker. If a speaker begins to roll-off at a given frequency, it can usually be attributed to inductance. If you can keep inductance low, you will have a wider bandwidth in which the speaker will play accurately.
NOTE: Le is a tricky parameter to compare. First, it varies with a number of factors, including frequency and power. When comparing various speakers using their published Le specification, be sure to divide the value of Le by the value of Re (the DC resistance of the voice coil). A speaker is a reactant load and an increase in Re will result in an increase in Le, though the corner frequency at which roll-off begins remains the same. In short, a speaker with a DC resistance of 4.0 ohms and an inductance of 2.0mH is actually better than a speaker with a DC resistance of 2.0 ohms and an inductance of 1.5mH.
So what is the key factor in the inductance equation? It’s almost exclusively the length of the voice coil. A longer voice coil will have higher inductance. A smaller voice coil will have lower inductance. Though inductance can be decreased through use of shorting rings or copper sleeves, the voice coil length is the primary variable when considering inductance.
Based on what we know so far, Split-Gap usually has the smallest coil, followed by Split Coil, followed by LMT. Let’s also consider the usability of shorting rings. The notch in the top plate of a Split-Gap design is very easy to fill with copper and help lower inductance. If you want to add copper to the gap in a Split Coil or LMT motor, you need to widen the gap, which drops your B, which drops your efficiency.
In terms of inductance, Split-Gap is the clear winner, followed by Split Coil, with LMT taking the last position.
Power Handling
Everything you just read above is transferable to the concept of power handling. A larger voice coil will usually handle more current, all other things considered constant. We know LMT has the largest coil, Split Coil has the second largest, and Split-Gap has the smallest coil. This is an easily understood concept: LMT is capable of handling the most power while Split-Gap has the lowest power handling capabilities.
Scalability
Some companies want to utilize a specific gap treatment for all their speakers. Use of those listed so far is most predominantly found in low frequency speakers, ie. subwoofers. The reason for this is obvious: to produce high SPL at low frequencies, you need a lot of linear excursion to achieve high displacement. At higher frequencies, less stroke is needed. So how easily can these gap treatments be utilized in other speaker designs?
Be sure you have looked at the pictures above and fully understand the concept. Part of the “scalability” of each gap treatment is the size of the motor for each. Though Split-Gap needs a taller top plate, the voice coil is very small and the motor is not very deep. LMT is similar in many respects to a standard overhung design, so large excursion requires a long voice coil, which means a very deep motor to accommodate. Split Coil follows the same concept. LMT also needs a wider motor than either of the two other gap treatments. So in terms of the sheer size of the motor required, Split-Gap will usually be the smallest.
The other concern is how easily the gap treatment is applied to the speaker. Imagine a tweeter with a 2mm tall voice coil. How easy will it be to vary the density of the coil in the gap? It won’t be very easy at all, and thus LMT proves to have little value here. Split Coil will work a little better, but the motor will be a bit deeper. Split-Gap will usually work the best here. However, it should be noted that the gap is so tight, the voice coil is so small, and the top plate is so short, that the advantages of any of these gap treatments are less visible for high frequency performance with small tweeters.
Overall, all three gap treatments are best suited for low frequency performance where high stroke is key. However, if you want to apply these treatments to smaller speakers for higher frequency performance, Split-Gap is probably your best bet.
Manufacturing Tolerances
When you’re building large-scale products where you are shipping pallets of speakers out, you want to make sure that nearly every speaker will measure the same and fall within the customer’s accepted tolerances. When you start fiddling with the motor, it becomes even more critical that these tolerances are met.
Split-Gap is probably the best here. It is very, very easy to machine the gap within very tight tolerances. Split Coil and LMT, on the other hand, prove to be a little more challenging. Controlling the positioning of the windings is not as easily achieved. Little changes in the number and location of windings can cause big issues with asymmetry of the BL curve, especially in LMT. If you take a look at the Eclipse SW8200 that was measured by npdang at DIYMA, you can see this very clearly.
Overall, Split-Gap likely has the easiest achieved tolerance, followed by Split Coil, with LMT third best.
Manufacturing Costs
Pretend you’re a manufacturer. You look forward to applying an intelligent new technology to your product. But what if this technology prices your product out of contention? At that point, selling your product proves to be more challenging. The lower you can keep your manufacturing costs, the more profit you can make, or alternatively, the lower you can price your product, making large volume sales more easily achieved.
As I have already mentioned, Split-Gap has higher costs for the top plate, especially with longer stroke. However, it also has a smaller voice coil. Split Coil has more voice coil length to it. LMT has a lot more voice coil length to it, and to achieve a given B, requires a wider and deeper magnet structure (because the gap is wider than normal to accommodate the windings). Split-Gap also has royalty/licensing fees you must pay if using that gap treatment.
Which is the least expensive to manufacture? Well, LMT is clearly the most expensive. In first place, it’s kind of a tie between Split-Gap and Split Coil. In many applications, production cost for Split-Gap will be lower, even with licensing fees considered. In very high excursion applications, you’ll probably find Split Coil to be less expensive.
Conclusion
As you can see, every gap treatment has its own inherit advantages and disadvantages. Each treatment has a particular application where it will prove to be more beneficial than the other options. So when should you use what? Well, here are my opinions.
Tweeters: None of the above. I’ll stick to an underhung design, thank you very much.
Midrange: Of the three, it would probably be Split-Gap that I would use. The low inductance helps give your speaker a wider bandwidth while still achieving good stroke. Split Coil can be utilized with good success, though you’ll need to put some copper in the motor to gain wide bandwidth.
Midbass: For a similar reason as above, the winners would be Split Coil or Split-Gap. Inductance is not as much of an issue for a speaker designed solely for midbass, so Split Coil might be my choice for the improved power handling the larger coil offers.
Subwoofer: This would probably be LMT or Split Coil for me. Both of them offer ridiculous stroke capabilities. Both have higher moving mass (which is great for increasing low frequency performance, manifested in a lower Fs). Inductance is of very little concern, as the inductive corner frequency usually falls above the bandwidth in which a subwoofer would be used.
Full Range: Split-Gap is the clear winner here. It’s capable of achieving good excursion for low frequency performance while keeping inductance low for high frequency performance. If you can overcome the cone breakup that is inherent in any full range design, you’ve probably got a winner. Split Coil isn’t an awful option here either, but it’s probably not your best choice.
Hopefully this helped answer some questions you might have about the linear BL gap treatments AND remove some of the bias you might have read in previous discussions. If you have questions or find an inaccuracy in anything above, please be so kind as to comment. I would love to hear other opinions or concerns.
Cheers,
Neil @ SSA
I will be adding the Differential Drive (aka Dual Gap) technology when I get a chance. Though it does allow for some flexiblity in terms of keeping BL linear, it shows more benefits in power handling by increasing surface area and air flow over the coil substantially.
The W7 is a very simple method: it's a standard overhung design with some machining done in the pole piece. If the right amount is done in the right places, you can achieve surprisingly linear BL, but it becomes increasingly more challenging to achieve this at very high levels of excursion. Of course, I'm of the opinion that a speaker that takes 1kW with 30mm of Xmax is more than enough for my ears.
I would like to thank Neil for this write up. In no way am i here to make him wrong, but im here to merely add some points from the inside perspective at least about our lms coils.
in general we use 4 layer round wire. Thats the most basic subwoofer coil. We that in our TC9's and TC2's for example.
An liner coil version does not have extra winding at the bottom or top, but rather a liner reduction made in the middle area to reduce BL product where the driver is most efficient. As a result, mass goes down and inductance does too, but the BL product (in particular the L component only) drops on average by a factor of 30 to 35%. The flux (telsa) density in the gap is identical to a non-linear version.
A linear voice coil is a horrible trade off if the driver is under motored, be it LMS or anything else really does need to use a larger motor to gain that back which makes it more expensive. This is in fact why our 4HP motor works so well. The motor is too powerful for any reasonable low frequency driver and it was a prefect candidate for a big LMS. In fact we had a few tight gap versions that pushed past a BL^2/Re of 550-600 and a Qts of ~0.08. Ya... you're not going to make any bass out of that, but at 60Hz tuning SPL burp, hold on tight! The 4" vc allows more steel inside the the t-yoke which prevents saturation to allow us to take advantage of a 10" magnet to get more B. The LMS 18" pushed close to 89dB at 1 watt and we already have plans to reduce nearly 100 more grams and increase the L component of the motor to push it past 90 with ease by next year.
Does it mean LMS is better? In fact, any of the above designs can be used with great success to linearize BL, but its really the implementation that makes the difference. I will say one great advantage of XBL is the sublet space in the motor where a shorting ring can fit. I can argue that inductance has very little affect on the response of an LMS in action below 100Hz, but non the less the shorting ring will improve linearity and make the speaker a better one then if it did not have it. That is something that can not be implemented in the other designs.
As far a tolerances. LMS is actually one of the most accurate. The BL curve is nearly flat and only deviats when the voice coils are offset (too low/high) as a result of a manufacfuring defect. In the case of the 8200, this was the case and its important for me to say that we did not manufacture any of the production units! We only made a few which were prototpyes and we outsouced the rest. There were defects and a major lawsuit ontop of that, that i can not get into. Lets just say we were not happy. In fact, even in a non-linear voice coil, an offset to the coil such as the early versions of the 8200 will a non-linear behavior as such. It was not specific to the linear coil at all. Not to point the finger elsewhere, but I have seen major deviations in XBL designs too where the BL curve was a double hump, rather than flat. Its important that any of the above, including non-linear high sensitivity designs be manufactured correctly.
credit:
Neil @ SSA
|